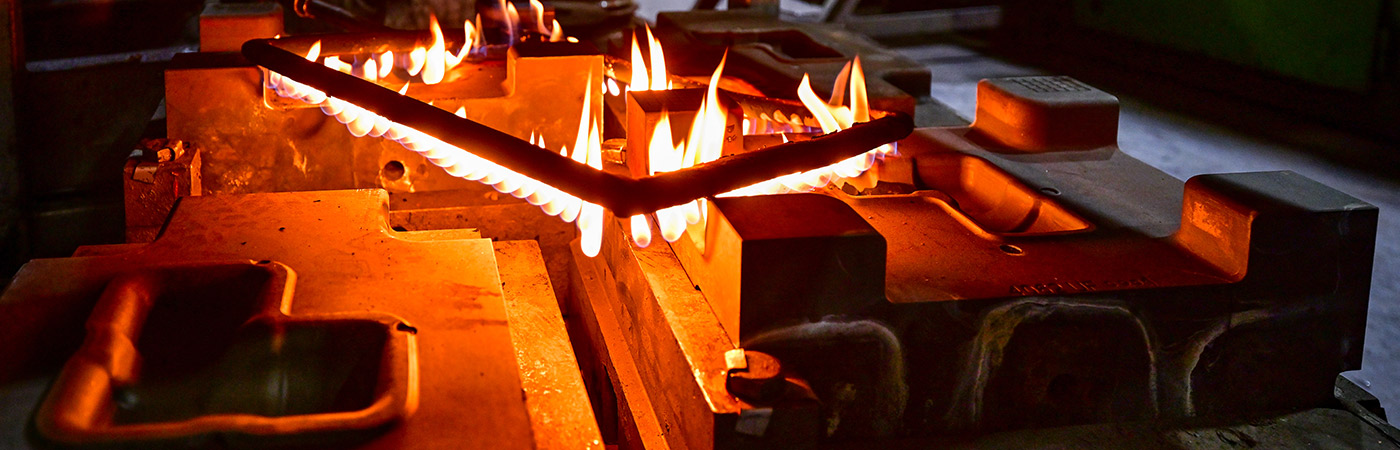
At the beginning was just steel. With this material Rasche is going to work. In the end we deliver a precision element ready to go into series production with the highest demands on functionality and stability. We build to individual demands. Only performance is what counts.
What do we need for this? Technical competence. Creativity. Experience. Teamwork. Equipment. Least but not least: System reliant trustworthy processes.
Development & design
The leading goal: maximum functionality
For complex challenges we find simple, elegant solutions: that’s good design service. Keeping in mind the complete spectrum of all boundary conditions: questions of geometry, design, material and finally calculation. We have a holistic approach to all development tasks
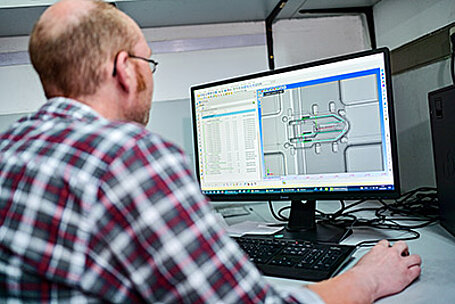
Besides trusted, automated systems for calculations and material simulation, we at Rasche are trusting our “creative heads“ in our team – experienced and innovative employees. We give them plenty of space for out of the box solutions. We support them with modern technology: from future oriented CAD software programs to up to date 3D printer to create prototypes – even with original material.
Constructing & Forging
Some call it warm forming. We call it forging.
The traditional way - although we are using modern technology. Because forging is heat, and with temperatures of over 1,200 Celsius, raw steel is exposed to during the forging process to produce a precision componence, it is exactly that: traditional forging.
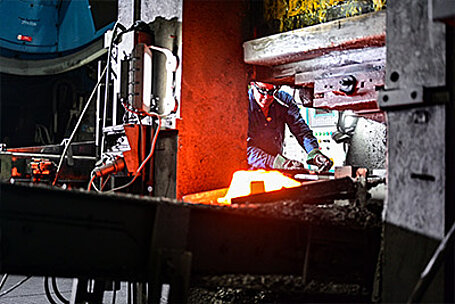
At Rasche the process chains are decidedly modern to reach this goal. All applications and punches are produced in-house. Reliable HSC machines, fully equipped welding stations and trendsetting measuring technology are available. We are in control of all steps and stages of the production process. And the forging itself – happens fully automated with the help of robotics.
Automation and standardization are indispensable ingredients of professional processes and proceedings. That also applies to Rasche. Flexibility, adaptability and moveability are what distinguishes the company. We are one of the few suppliers that on demand supply short runs from 1,000 pieces reliable and efficient. In addition to providing solutions, we are responding to individual demands.
data sheet
- Half automated and fully automated forging presses
- Press load from 1,600 to 3,150 tons
- Billet weights of forging blanks from 0,2 to 18 kilogram
- Processing of high-alloy-steels as well as titanium
Perfecting & Assembling
Ready for the finishing touch
An integral part of our production process is the mechanised final processing, finishing and controlling of the required components. Turning, drilling, grinding and milling – in our finishing department every detail counts. And above all: the perfect, ready to use machining. Four spindles taking care of this.
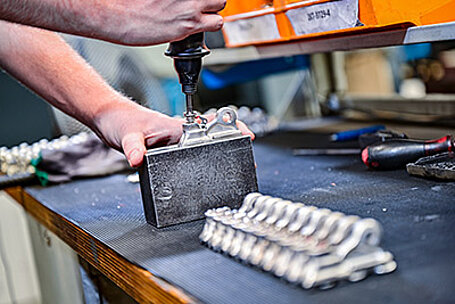
Impurities of the final product will be eliminated at Rasche with the support of a modern sandblasting system. For the final control and examination of the components we use machines that - with the help of the magnetic particle method for the metallurgical test work - to point out potential errors and cracks. Because that’s not enough for us, additionally we add a qualified manual control of visual checks. Nothing is left to chance.
To give the surface of our components a durable protection, Rasche works with a range of certified suppliers. Depending on requirements and application, the final product can be nickel-plated, chromed, nitrided, varnishing, galvanized or given a coat of synthetics.
If required we also offer up to the final assembly of components.
Assemblies and facilities for the finishing touch
- Calibration presses with 1,000 tons of pressing force
- For compaction of surfaces
- For forming in specific tolerances
- For embossing complex contours and lettering
- Sandblasting for removal of impurities
- Crack detection machines (magnetic powder process)
- Turning and milling center with workpiece station
- Machining center
- 3D measuring machines to optimize assembly process
- Assembly center